 |
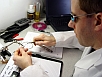
by Professor String |
Ten differences in plain steel guitar strings you should
know
|
When talking about the unwound (plain) steel strings that are
typically smaller than twenty gauge diameter there is a popular
opinion amongst guitarists. Many claim they cannot hear a
difference in sound between these strings brand-to-brand. In
fact, the difference between a .009 and .011 gauge string tuned
to the same note is challenging to decipher regardless of brand.
Yet, when we start talking about the difference in "feel"
between these two gauges, there is something to be noticed. The
heavier string is much stiffer when you try to bend it, or press
it against the fret. This now leads us to the big question...What
is the difference in brands when it comes to these plain steel
strings? Some seasoned guitarists claim the difference in brands
is mainly found in the wound strings. They feel the plain steel
strings are pretty much the same from brand-to-brand. We can be
sure the string manufacturers would care to differ, "Buy our
strings and not theirs, because our plain steel strings are
[insert product claim here]."
Let us consider a plain steel .009 gauge E-string for a moment.
For those of you who use an extra light gauge E-string, and bend
it almost over the neck, you already know that this string goes
through a lot. For rockers, this string is the screamer. It is
the string that must work during the solo. A guitar without this
screaming wire is like a guitar with a sore throat. It is
totally the upper range. This is a string (like others) that
needs to meet our expectations. As soon as that string fails it
is a serious bummer. There are some manufacturers who include an
extra E-string in their sets. This is somebody who wants to make
sure you are covered in the event of premature breakage. It can
mean their lack of confidence in the product is possibly in
question. In either case, the effort is noble. It is an effort
to make sure your expectations are met for that plain steel
string. Quality is about being able to do something correctly
and repeatedly without deviating anything. Making a quality
plain steel string is all about that. That means the following:
1. It must stay in tune - Poor metallurgical processing
of musical wire can create a real disaster for the tunability of
a very thin string. This is something that is not easily caught
with each individually created string at the factory. The
elasticity of the string plays a factor, and time will only tell
if it will have stability under tension.
2. It must not prematurely break - Yeah, I know. This
sounds like a no brainer. Of course it should not break upon the
first strum. It happens. I like asking people what they do about
it when they go to replace the string (or entire set!). I hear
anything from "No problem. Got a spare right here," to "Holy
crap I spent a lot of money on the set. I'm never buying that
brand again." Notice that last response goes to show how quickly
brand loyalty can disappear in the string business. One bust,
and your brand is a bust.
3. It must have clarity - When we talk about clarity we
are talking about not only tone, but the overall sound quality.
Does the string sound crisp and not like a sitar? Even gauging
and plating are something that plays a factor. Really crisp
clean clarity will produce a twang or wire-like sound. Some
folks like the sound of their strings only after they have been
played a few times. Basically a break-in period to knock down
some of that new string shimmer.
4. It must carry a delicate harmonic when needed - This
is something that is very noticeable amongst different brands of
plain steel strings. It is not purely a function of the
instrument's bridge, nut, neck,...etc. Some of the attributes to a
string's harmonic tone come from metal purity, even plating and
even gauging to name just a few. A good test when benchmarking
plain steel strings is to strike a solid 3rd fret harmonic. A
well made plain steel string will ring out clearly with smooth
and even decay. In fact, it will be very forgiving if the player
does not hit the harmonic solid on the first strike. A poorly
made plain steel string will barely carry the harmonic and have
rapid decay as soon has the harmonic is struck.
5. It must play easily ' When fretting, a string with
great elasticity will go a little easier on the finger tips. It
will stretch a little easier, and allow less finger pressure.
Yes, gauge thickness has much to do with this trait, but so does
the ability for the string to ring when it is not firmly pressed
in between frets. How about those knuckle busting chords with
your pinkie finger stretched way out there? A string with some
"give" will ring out if your pinkie is straining to press that
note.
6. It must carry upper register frequency - Simply
stated, the string should not sound like it has been dipped in
rubber cement. This is one of the reasons we do not see many
polymer coated strings on plain steel strings. The thin coating
has a harmonic dampener effect that knocks out upper register
frequencies.
7. It must carry sustain when needed - This is important
and is not solely based on the instrument's construction. The
test here is simple. How long will the string produce a sound in
open position and fretted positions? Some of you might respond
by thinking you can simply turn up the gain on the amp to
compensate. Shame on you. The people on acoustics might have a
few words for you on this topic.
8. It must have a smooth feel - Ah, that wound string
squeak we all recognize (and sometimes hate during recording).
Well, it is not just the wound strings that can cause squeak. A
good plain string will have a nice polished surface prior to its
plating process.
9. It must have a proper ball-end twist - If you have a
bridge that does not require the ball-end to be cut off, pay
attention to this detail. Not all ball-end twists are the same
from brand-to-brand. Some are twisted tighter/looser, have silk
on them, or simply use a different style of ball shape. In fact,
this could be whole discussion of its own. If you have not
compared the different ball-end twists of various brands, you
should make a point of doing it. This simple twist at the end of
every plain steel string is a big deal to some who claim it
affects everything from tuning to sustain. Bottom line: Know the
twist. No pun on Chubby Checker here!
10. It must have protective plating on it - Something
rarely discussed is the plating applied to plain steel strings.
Most plain steel strings have a protective plating of tin on
them, or nickel. This must be uniform and have bright luster up
and down the entire length. If it is not correctly plated it
will have tarnish spots unevenly where the base metal is
exposed. In addition, the uneven plating will actually have an
effect to the tone.
Right out of the gate, there are ten things this string needs to
do. Should you take for granted that this string will do it when
you pull it out of the package? If so, what makes you confident?
Is it the story of the brand or is it something else? In taking
a closer look at the ten things we have evaluated in a plain
steel string, we can see there is much more than meets the eye
with this string. They are not all created equal.
Best Wishes,

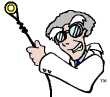 |
Looking to learn more about
guitar strings and bass strings? Go Here
Do you have some thoughts about
this article or the subject? Share it with everyone on
the Professor's
Forum. |
|